Being Proactive is the Best Defense.
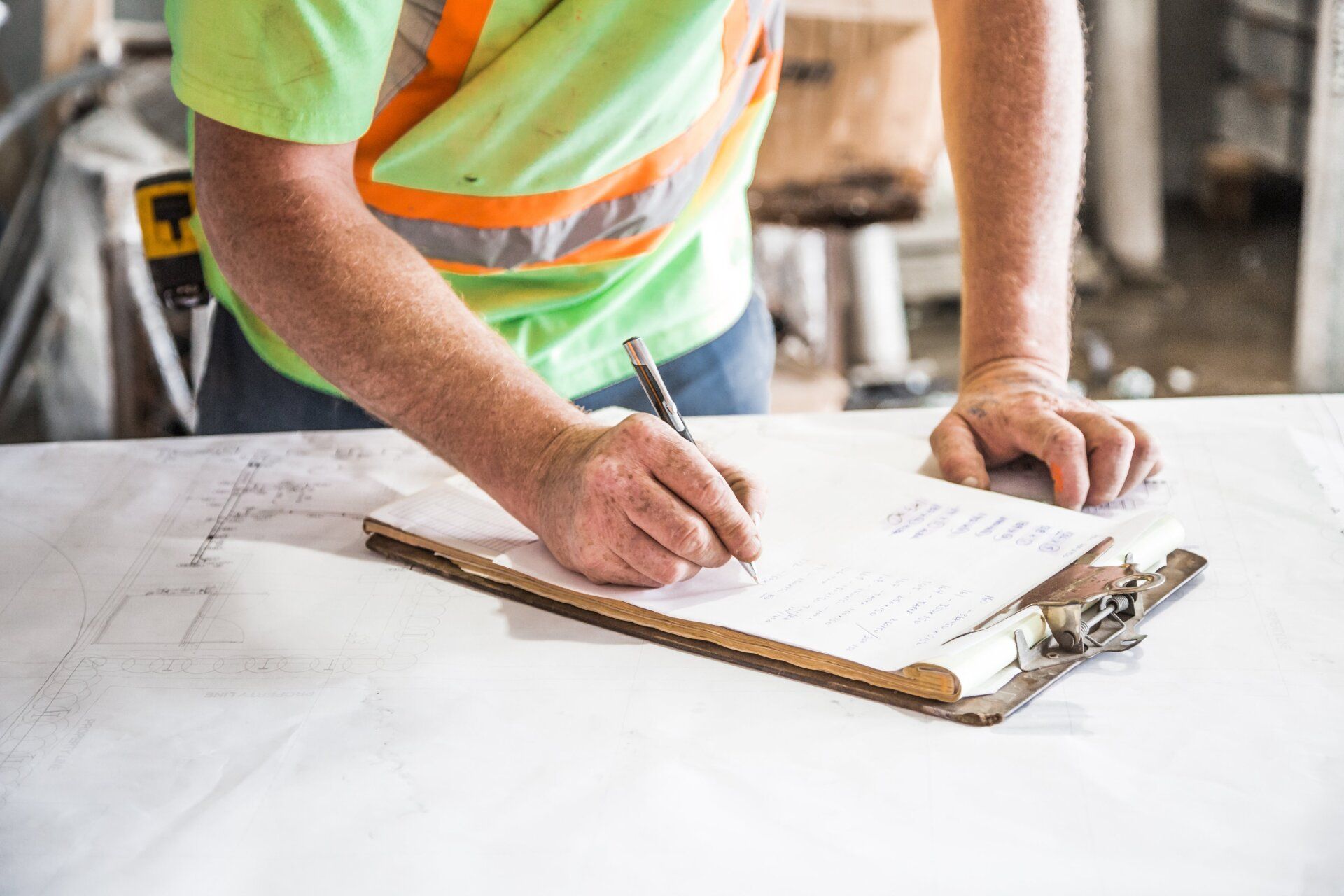
What is Failure Mode and Effects Analysis (FMEA)?
Failure Mode and Effects Analysis (FMEA) is a systematic, proactive method for evaluating a process to identify where and how it might fail and to assess the relative impact of different failures. It was first developed by the U.S. military in the 1940s as a way to prevent potential problems from occurring in their designs.
Today, FMEA is used widely across many industries, including manufacturing, healthcare, automotive, aerospace, and more. It's an essential tool for small business owners who want to refine their production processes and ensure the highest quality products are produced with minimal risk of failure.
How Can Small Business Owners Use FMEA?
Small business owners can use FMEA to identify potential failure modes in their design or process before they occur. This helps them reduce the risk of costly mistakes or product defects that could lead to customer dissatisfaction or even legal action. By proactively identifying potential problems before they arise, small business owners can save time and money while improving product reliability and quality management.
FMEA also helps small business owners estimate costs more accurately by taking into account all possible failure modes that could occur during production. This allows them to better plan for future growth and streamline their supply chain processes for maximum efficiency.
Steps For Implementing FMEA Effectively
- Identify all components, assemblies, subsystems, etc., that could potentially fail during production
- Assign a severity rating to each potential failure mode based on its impact on customers or other stakeholders
- Assign an occurrence rating based on how likely it is that each failure mode will occur
- Assign a detection rating based on how easy it is to detect each failure mode
- Develop corrective actions for each identified failure mode
- Monitor performance regularly and adjust corrective actions as needed
Actionable Tips & Best Practices
Here are some tips for small business owners looking to implement FMEA effectively:
- Involve team members from all departments when conducting an FMEA analysis so everyone has a clear understanding of what needs improvement
- Prioritize corrective actions based on severity ratings so you can focus your efforts on areas with the greatest risk of failure first
- Establish regular monitoring procedures so you can track performance over time and make adjustments as needed
- Utilize real-world examples and case studies from other companies who have successfully implemented FMEA
- Leverage technology such as automated software tools when available for improved accuracy
Failure Mode and Effects Analysis (FMEA) is an essential tool for small business owners who want to refine their production processes and ensure the highest quality products are produced with minimal risk of failure. By proactively identifying potential problems before they arise, small business owners can save time and money while improving product reliability and quality management at the same time. With careful planning, implementation of best practices, and regular monitoring procedures in place, small businesses can use FMEA effectively drive future growth while streamlining their supply chain processes for maximum efficiency!
Have a Question? Ready to Integrate FMEA into your business? Schedule a Free Consultation With Us.