Responding Effectively Can Make the Difference.
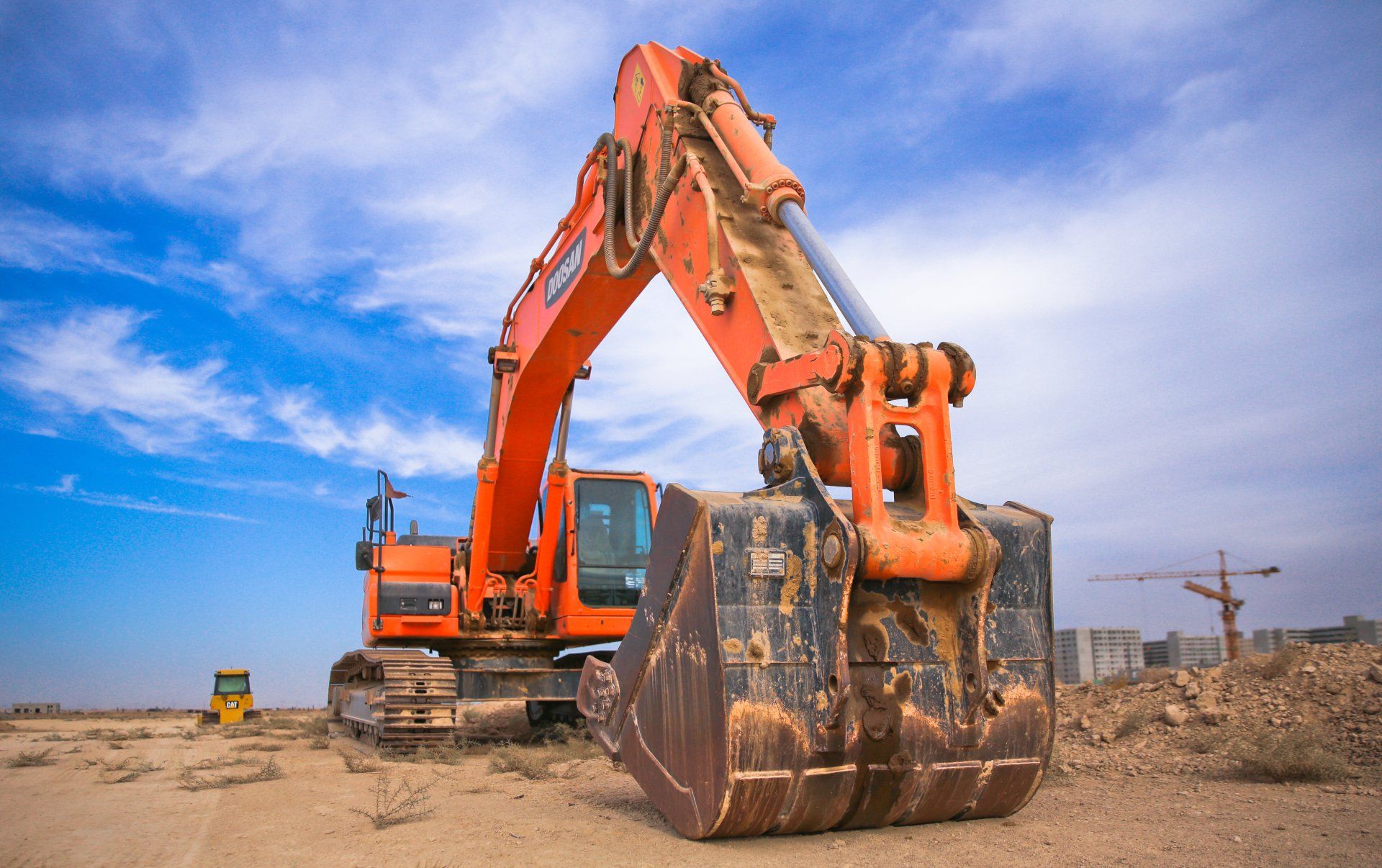
When a critical piece of equipment malfunctions, it can disrupt your operations, impact your bottom line, and even jeopardize customer satisfaction. To mitigate these risks, it's essential to have a structured process for investigating equipment failures.
In this guide, we'll walk you through the steps to effectively diagnose and address equipment failures in your business.
Stay Calm and Ensure Safety
When equipment fails, emotions can run high, but it's crucial to remain calm and composed. Your first priority is safety. Ensure that no one is in immediate danger due to the equipment failure, and if necessary, secure the area or evacuate it. Safety always comes first.
Document the Incident
Begin the investigation process by documenting the incident. Record the date, time, and location of the equipment failure. Take pictures or videos of the affected equipment and the surrounding area. This documentation will be valuable for insurance claims and future reference.
Identify the Equipment and Its Criticality
Determine which piece of equipment has failed and its importance to your business operations. Is it a critical component, a minor tool, or something in between? Knowing this will help you prioritize your response and allocate resources accordingly.
Assemble a Response Team
Gather a team of employees who are knowledgeable about the equipment in question. If necessary, include external experts or technicians who can provide insights into the failure. Collaboration is key to a thorough investigation.
Analyze the Equipment's History
Review the maintenance and repair history of the equipment. Have there been any recent repairs or modifications? This information can provide clues about the root cause of the failure.
Examine Operating Procedures
Ensure that your team is following the correct operating procedures for the equipment. A failure might result from human error or negligence. If necessary, provide additional training or updates to your standard operating procedures.
Inspect for Physical Damage
Examine the equipment for physical damage or wear and tear. Look for signs of overheating, corrosion, loose parts, or any other visible issues. Sometimes, the cause of the failure is evident through visual inspection.
Review Environmental Factors
Consider environmental factors that might have contributed to the failure. Temperature, humidity, dust, and other conditions can affect equipment performance. Make sure the equipment is operated within the manufacturer's recommended environmental parameters.
Check for Software or Electrical Issues
If the equipment relies on software or electronics, investigate whether software glitches or electrical problems might be the root cause. Ensure that all software and firmware are up to date, and inspect electrical connections and circuits for any irregularities.
Consult Manufacturer or Supplier
Contact the equipment's manufacturer or supplier for guidance. They can provide valuable insights, troubleshooting advice, and recommendations for repair or replacement. Keep records of all communication with them.
Implement Preventive Measures
Once you've identified the cause of the equipment failure, take steps to prevent it from happening again. This might involve more regular maintenance, equipment upgrades, or changes in operating procedures.
Review Insurance Coverage
Check your insurance coverage to see if the equipment failure is eligible for a claim. If applicable, file a claim promptly to help cover repair or replacement costs.
Develop a Contingency Plan
Incorporate the lessons learned from the equipment failure into your business continuity plan. Having a contingency plan in place can minimize downtime and financial losses during future incidents.
Monitor and Learn
Continuously monitor your equipment and gather data to identify trends and potential issues before they become failures. Learning from past failures is key to improving your business's resilience.
Remember that equipment failures are a part of doing business, but how you respond to makes the difference. By following these steps and maintaining a proactive approach to equipment maintenance, you'll be better equipped to keep your small business running smoothly and minimize the impact of equipment failures on your operations and profitability.
Need to implement an Equipment Failure Investigation Process for your business? We're here to help. Schedule a free consultation.