Movement is More Important Than You Think
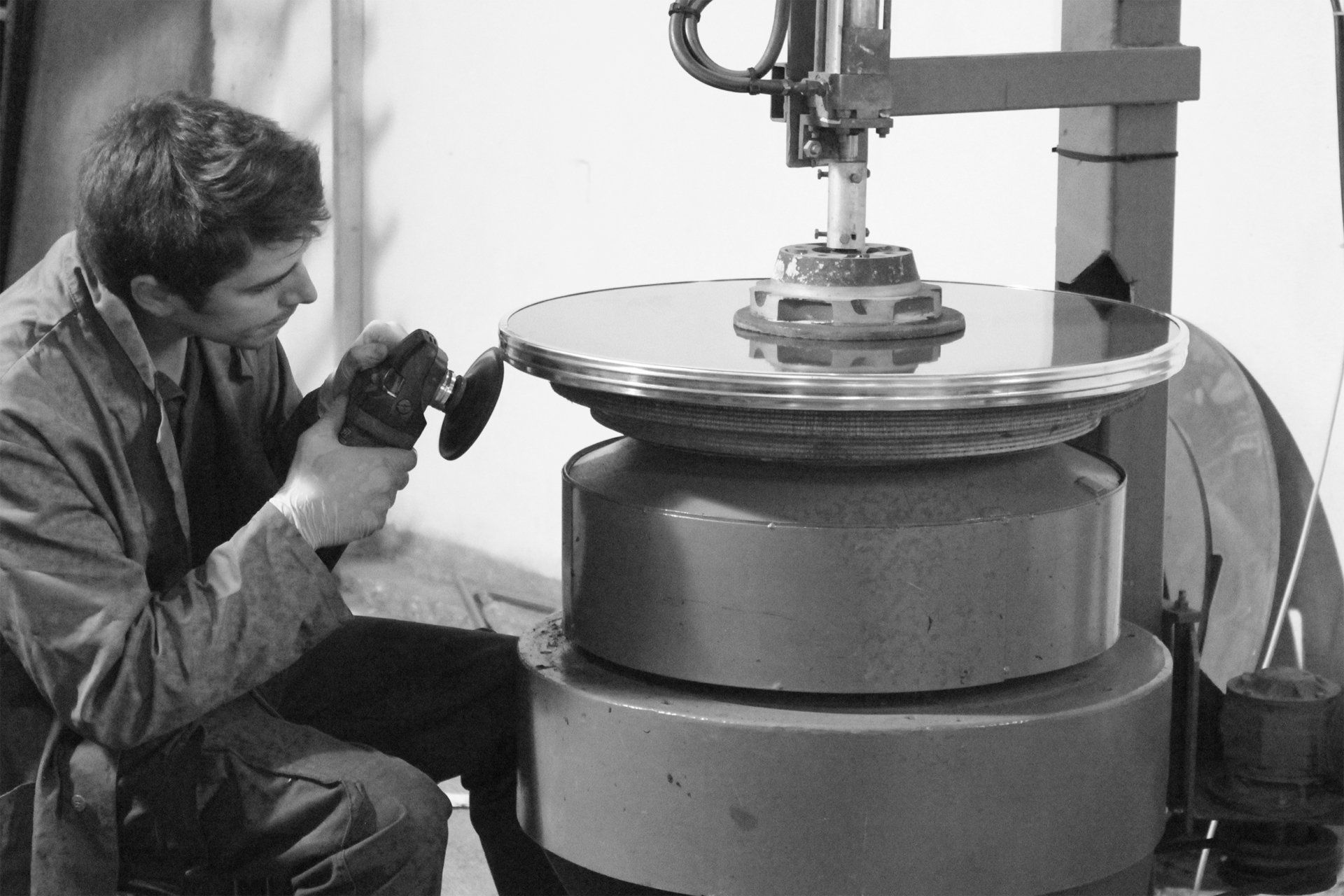
In the world of small business, efficiency is the name of the game. Whether you're manufacturing products, providing services, or managing a retail operation, minimizing waste in your production processes can significantly impact your bottom line. One common source of waste that often goes unnoticed is movement waste. This type of waste occurs when unnecessary movements or activities slow down your production line, increase operational costs, and decrease overall productivity.
Understanding Movement Waste
Movement waste, also known as motion waste, is one of the seven types of waste identified in lean manufacturing principles. It refers to any unnecessary physical movements or actions performed by employees, machinery, or equipment that do not add value to the final product or service. These non-value-added movements can include excessive walking, searching for tools or materials, reaching for items, and redundant steps in a process.
The Impact of Movement Waste
The consequences of movement waste can be detrimental to your small business:
Increased Labor Costs: Unnecessary movements lead to increased labor costs as employees spend more time on tasks that don't contribute to the product or service's quality.
Reduced Productivity: Movement waste slows down production processes, leading to longer lead times and decreased output
.
Higher Risk of Errors: More movements increase the chances of errors, defects, and accidents, which can negatively affect product quality and customer satisfaction.
Lower Employee Morale: Excessive and non-value-added movements can lead to employee frustration, dissatisfaction, and burnout.
Wasted Resources: Time, energy, and resources that could be better allocated elsewhere are wasted on unnecessary movements.
Tips for Eliminating Movement Waste
Conduct a Value Stream Mapping (VSM) Analysis: Start by mapping out your production process to identify areas with the highest occurrence of unnecessary movements. VSM can help you visualize your processes and pinpoint areas for improvement.
Standardize Work Procedures: Develop standardized work procedures that outline the most efficient way to complete tasks. Make sure employees are trained and follow these procedures consistently.
Organize Workstations: Organize workstations to minimize the need for employees to move around excessively. Place tools, materials, and equipment within easy reach to reduce reaching and searching.
Implement 5S Principles: The 5S methodology (Sort, Set in order, Shine, Standardize, Sustain) focuses on workplace organization and cleanliness. Applying these principles can help reduce movement waste by ensuring that everything has its place and is easily accessible.
Use Technology Wisely: Consider investing in technology and automation where appropriate to reduce manual tasks and movements. Robotics, conveyor systems, and software can streamline processes and minimize human intervention.
Involve Employees: Your employees are valuable resources for identifying and eliminating movement waste. Encourage them to provide suggestions and feedback on improving work processes.
Monitor and Measure Progress: Regularly track key performance indicators (KPIs) related to movement waste reduction. Continuously analyze data to identify areas that still need improvement.
Continuous Improvement Culture: Foster a culture of continuous improvement within your organization. Encourage employees to seek out and eliminate movement waste as part of their daily responsibilities.
Eliminating movement waste in your production processes is a crucial step toward achieving operational excellence in your small business. By identifying and addressing unnecessary movements, you can boost productivity, reduce operational costs, and enhance the overall efficiency of your operations. This process is an ongoing effort, and a commitment to continuous improvement will help you stay competitive in today's business landscape.
Ready to streamline your operations? Give us a shout! Schedule a Free Consultation