Is It Time for New QC Measures?
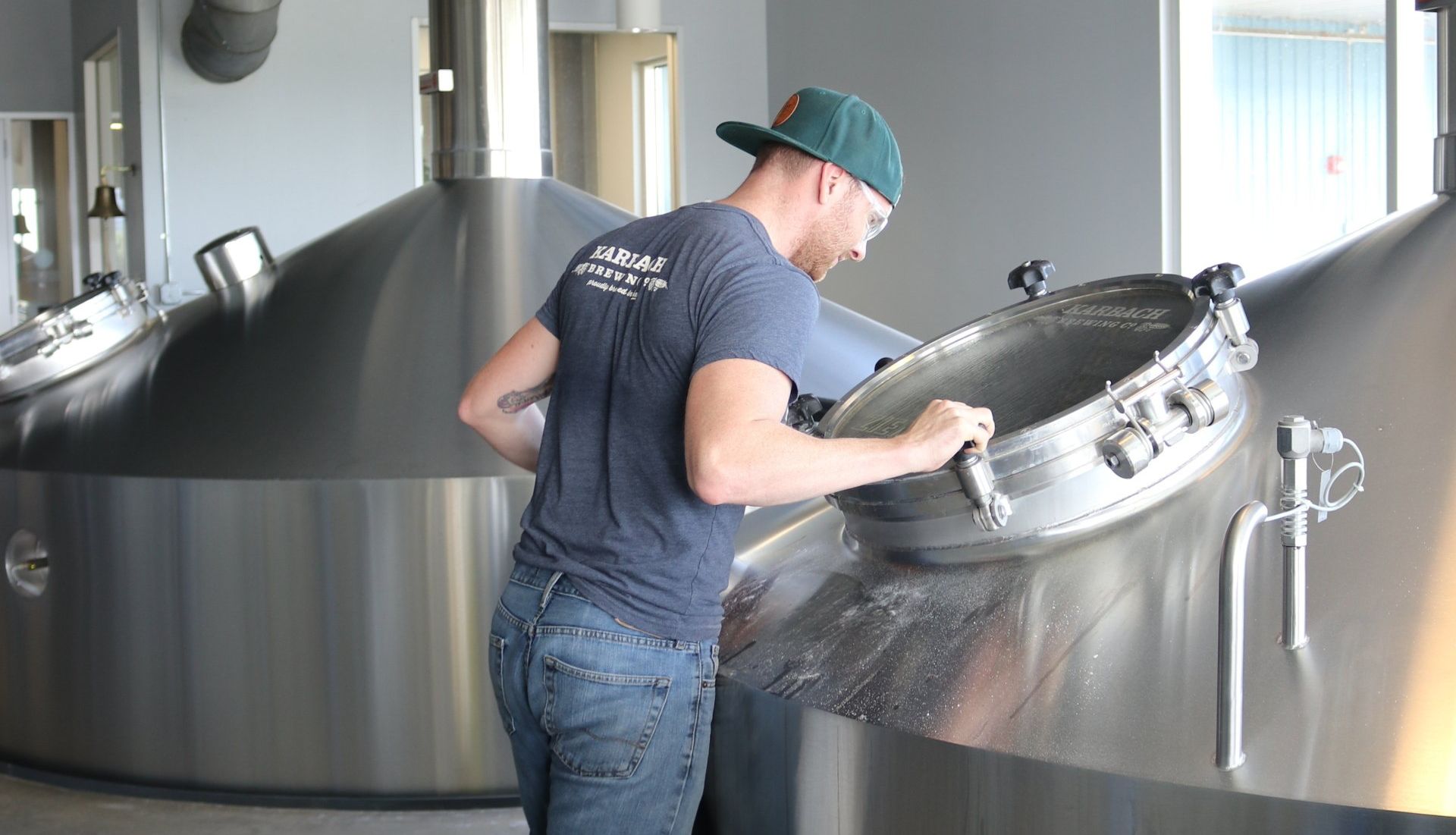
As a small business owner, you know that quality control is essential for success. Quality control measures do more than just help ensure that your products and services meet customer expectations, they also help you identify potential problems before they become costly issues. We're covering the importance of quality control for small businesses and providing a roadmap with actionable steps for setting up a quality control process in your own business.
What is Quality Control?
Quality control (QC) is the process of ensuring that products and services meet certain standards of quality. It involves inspecting, testing, and evaluating products or services to make sure they meet predetermined criteria. QC can be applied to any product or service, from manufacturing goods to providing customer service.
The goal of QC is to identify and address potential problems before they become costly issues. By implementing effective QC processes, businesses can reduce waste, improve customer satisfaction, and increase profits in the long run.
Signs You Need Quality Control Processes
There are several signs that indicate a need for quality control processes in your business:
- Defective products: If you're noticing an unusually high number of defective products coming out of production, it's time to implement QC measures. This could include inspecting each product before it leaves the factory or conducting regular tests on materials used in production.
- Ongoing complaints from customers: If customers are consistently complaining about the same issue with your product or service, it's likely due to a lack of QC processes in place. Taking steps such as conducting customer surveys or focus groups can help you identify areas where improvements need to be made.
- Negative reviews: Negative reviews can have a huge impact on your bottom line. Regularly monitoring online reviews can help you spot trends that may indicate an underlying problem with your product or service that needs attention from a QC standpoint.
How To Set Up A Quality Control Process
Setting up an effective quality control process doesn't have to be complicated or expensive; there are several simple steps you can take right away:
- Determine Your Quality Standards: Start by establishing what constitutes "quality" in terms of your product or service offering; this will serve as the foundation for all other QC measures you put into place.
- Develop A Well-Designed Operational Process: Once you've established what "quality" means for your business, create an operational process outlining how employees should go about meeting those standards on a daily basis; this should include detailed instructions on how tasks should be performed and what materials should be used during production/service delivery etc..
- Provide Specific Training To Employees: Make sure all employees understand the importance of meeting quality standards and how their individual roles contribute towards achieving them; provide training sessions so everyone knows exactly what is expected of them when it comes to producing/delivering high-quality products/services.
- Review Your Process And Make Adjustments As Needed: Regularly review your operational process and make adjustments as needed based on feedback from customers, employees, etc.; this will help ensure that your QC measures remain relevant and effective over time.
Quality control is essential for small businesses looking to succeed in today's competitive market; it helps ensure that customers receive consistent high-quality products/services while helping businesses reduce waste and maximize profits in the long run. By following the steps outlined above, small business owners can begin to set up their own effective quality control processes without breaking the bank!
Ready to design a new, effective QC process for your business? Schedule a Free Call With Us